Double crank stamping punch press is a kind of equipment used for metal stamping processing, especially suitable for processes that require high precision and large-scale production. Its core feature is the use of a double crankshaft drive system, which can provide a smoother and more uniform pressure output compared to traditional single crankshaft stamping presses, reducing mechanical vibration, improving production efficiency and stamping quality.
Double crank stamping punch presses are widely used to manufacture large-sized and complex-shaped metal parts such as automobile shells, doors, roofs, chassis, etc. These parts require high precision and large-scale production, and double crankshaft punch presses provide stable and uniform pressure to ensure the quality of forming. Such as the stamping of engine covers, fuel tanks, exhaust pipes and other parts. These parts require strong pressure and precise forming, and double crankshaft stamping punch presses can ensure high-precision and high-strength production requirements.
Metal shell manufacturing: such as the shells and structural parts of household appliances such as refrigerators, washing machines, and air conditioners, usually need to be produced by stamping technology. Double crankshaft punch presses can accurately control the stamping process, reduce material waste, and ensure efficient production. Double crank stamping punch presses are also used for stamping small motors and electrical appliance housings to meet the needs of the home appliance industry for high-precision, small-batch production.
Double crank punches can be used to stamp various precision metal parts, such as connectors, shielding covers, terminals, etc. These parts usually require high dimensional accuracy and smooth surfaces. Double crank punches provide a smooth pressure output to ensure processing quality. When producing metal housings for batteries such as lithium batteries, double crankshaft stamping presses are also often used to stamp metal housings to ensure the uniformity and compressive strength of the housings.
The metal structural parts of aircraft usually have complex shapes and strict quality requirements. Double crankshaft stamping presses can be used to stamp these high-strength and precision metal parts. The stamping of parts such as the housing and bracket of aircraft engines also relies on double crankshaft punches, which can provide uniform pressure, reduce stress concentration, and thus ensure the structural stability of the parts.
In the production of some precision molds, double crank stamping punch presses can ensure the accuracy of the shape and size of the molds, and are widely used in medical equipment, precision instruments, watch manufacturing and other fields. For some small-sized and complex-shaped metal parts, the double-crank punch press can also achieve high-precision punching and forming.
The double-crank punch press can accurately cut, form, punch and other operations on thin and thick plates, and is widely used in industries such as construction and metal manufacturing. In some assembly industries, such as furniture, mechanical equipment, etc., the double-crank punch press is used to manufacture complex structural parts, which require high dimensional accuracy and good appearance.
Advantages of double-crank punch press:
Due to the double-crank design, the machine can provide more uniform pressure output, reduce mechanical vibration, and thus improve processing efficiency and production quality.
Compared with traditional single-crank punch presses, the double-crank punch press has a smaller impact load and lower loss to equipment and molds.
The uniform pressure of the double-crank punch press makes the mold force more uniform, thereby extending the mold. The double-crank punch press can adapt to metal materials of different thicknesses and hardnesses, and has shown good performance in the processing of a variety of materials.
In summary, double crank stamping punch presses are widely used in various fields that require high precision and large-scale production, especially in the automotive, home appliances, electronics, aerospace and other industries, where there are high requirements for production efficiency and component quality.
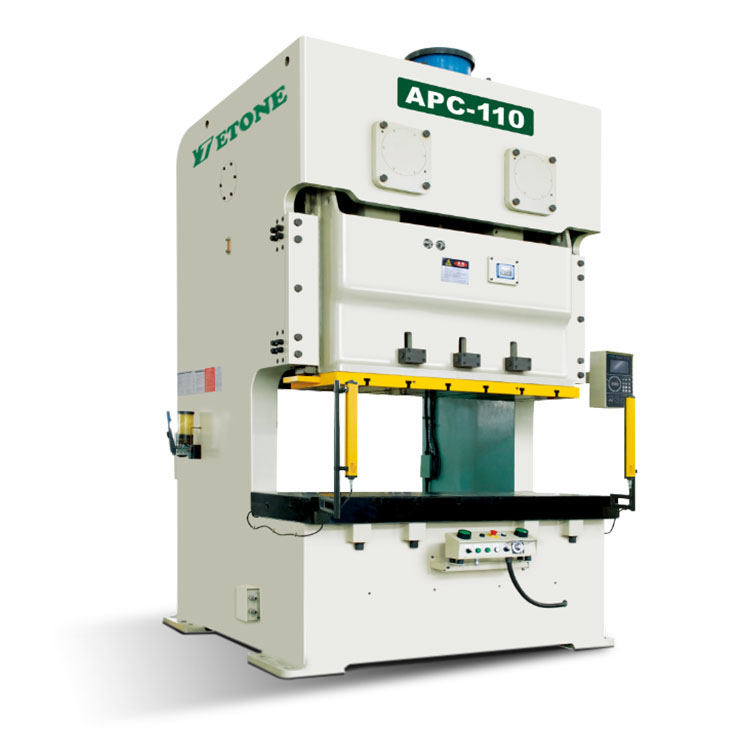