High-precision power presses play an important role in industrial manufacturing and processing, especially in applications that require precision operation and high loads. It has some certain advantages, as follows:
High-precision control: High-precision power presses are equipped with advanced control systems and sensors, which can achieve very fine pressure control, ensuring that the accuracy of each pressure application is very high, especially suitable for precision manufacturing, mold forming, parts processing and other demanding occasions.
High repeatability and stability: Due to its precise control system and mechanical design, the power press can maintain stable pressure output in continuous operation, ensure product consistency, reduce process errors, and is especially suitable for mass production.
Versatility: Modern high-precision power presses can be adjusted under different process requirements, support a variety of operation modes, such as stamping, pressing, stretching, etc., to adapt to a variety of different production tasks.
Energy saving and efficiency: High-precision power presses are usually designed as energy-efficient equipment, which can improve production efficiency and reduce operating costs by optimizing energy utilization and reducing unnecessary energy waste.
Automation integration: High-precision power presses can be integrated with automated production lines, and cooperate with robots, conveyor belts and other equipment to achieve fully automated production, improve production efficiency, reduce labor costs, and reduce human errors.
Reduce process defects: High-precision control helps to reduce product deformation, cracks or other defects caused by uneven pressure and improve product quality.
Therefore, the advantages of high-precision power presses are mainly reflected in precision control, repeatability and stability, as well as adaptability to high-demand production environments, and are suitable for complex processes with high precision requirements.
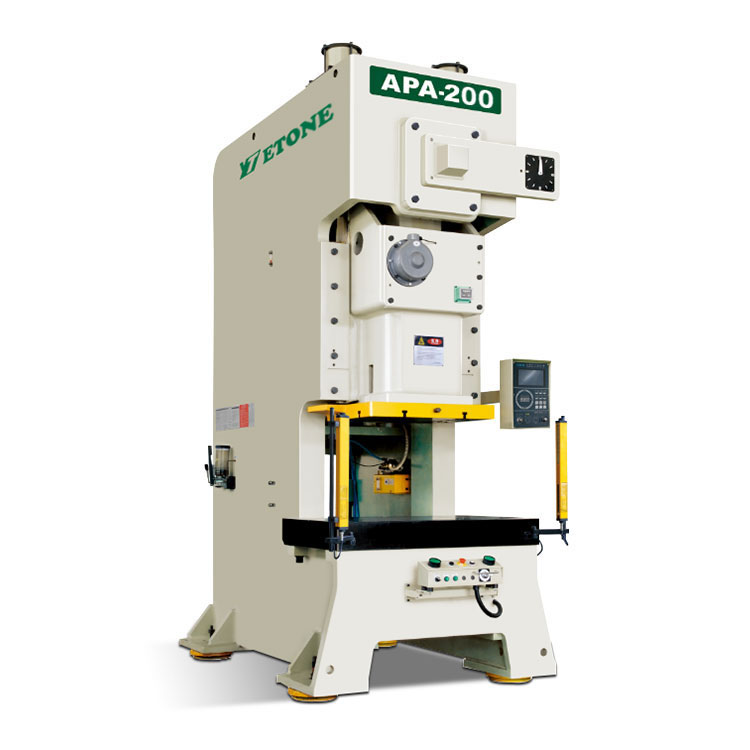