Check whether the double crank press is operating normally, which can be checked from multiple aspects. Here are some common inspection steps:
1. Visual inspection
Appearance inspection: First check the appearance of the machine to ensure that there is no obvious mechanical damage, cracks, oil stains, abnormal wear, etc.
Oil leakage: Check whether there is leakage in the oil pipe, joints, oil seals and other parts, and whether the hydraulic oil is sufficient.
Noise: Pay attention to whether the machine makes abnormal sounds when running. Under normal circumstances, the sound of the press should be stable when running. If there is a collision, friction or other abnormal noise, there may be a problem with the internal parts.
2. Hydraulic system inspection
Oil temperature: Check whether the temperature of the hydraulic oil is within the normal operating range. Too high oil temperature may cause the hydraulic system to fail, and too low oil temperature may cause the oil viscosity to be too high, affecting the efficiency of the hydraulic system.
Oil level and oil quality: Check the oil level of the hydraulic oil to ensure that the oil volume is sufficient and the oil should not have contaminants or too much water. Change the oil regularly to keep the oil quality good.
Pressure gauge inspection: Check the pressure gauge of the hydraulic system to ensure that the pressure is within the specified range. Abnormal pressure in the hydraulic system may affect the normal operation of the press.
3. Mechanical system inspection
Crankshaft inspection: Check the crankshaft for abnormal wear or damage. Ensure that the crankshaft does not deviate or make abnormal noise during operation.
Connecting rod and pin inspection: Check the connecting rod, pin and other parts of the press for wear, looseness, cracks and other problems.
Flywheel and drive part: Check the flywheel, belt, gear and other drive parts to ensure that they are not loose, worn or damaged, and are well lubricated.
Slide and guide rail: Check the wear of the slide and guide rail to ensure that they run smoothly, and lubricate or replace them if necessary.
4. Electrical system inspection
Motor and electrical control system: Check the operation of the motor to ensure that there is no overheating, abnormal noise or failure. Check the electrical control panel to ensure that the wiring is firm and there is no looseness or electrical failure.
Control signal: Check the control system of the press to ensure that the sensors, buttons and switches are working properly, and whether the detection system can accurately feedback the operating status of the press.
5. Operation performance inspection
Start and stop: Start the press and check whether it can start and stop smoothly. There should be no abnormal conditions such as jamming, abnormal noise or vibration during startup.
Movement stability: Check whether the press moves smoothly and whether the slider rises and falls smoothly. Avoid jitter, jamming and other conditions during operation.
Pressure control: Check the pressure control system of the press according to the use requirements to ensure that it can reach the set pressure and remain stable.
6. Safety device inspection
Emergency stop device: Check whether the emergency stop button and related safety devices are sensitive to ensure that they can stop in time in an emergency.
Limit switch: Check whether the limit switch is working properly to prevent the movement of the press from exceeding the predetermined range and causing mechanical damage.
7. Vibration and temperature monitoring
Vibration test: Use vibration monitoring equipment to detect the vibration of the machine during operation. Vibration beyond the normal range may indicate problems with bearings, gears or other components.
Temperature monitoring: Use infrared thermometers or sensors to check the temperature of key parts. Abnormal temperature rise may mean that the component is faulty or insufficiently lubricated.
8. Pressure test
Load test: Load the press step by step to observe whether it can smoothly withstand the set load and check whether there is obvious deformation or abnormal noise.
Pressure stability: Check whether the hydraulic system can stably output the required pressure, especially whether there is pressure fluctuation under high load conditions.
9. Record and analysis
Operation log: Regularly check the operation log and maintenance record to ensure that the maintenance and maintenance of the machine are handled in a timely manner to prevent equipment problems caused by long-term non-maintenance.
Historical fault analysis: If the machine has failed, analyzing the historical fault records can help to find possible fault points in advance.
Summary: Detecting whether the double crank press is operating normally requires a comprehensive inspection from multiple angles such as hydraulic system, mechanical components, electrical control, operating performance, vibration and temperature monitoring. Regular inspection and maintenance are the key to ensuring the normal operation of the press and extending its service life. At the same time, keeping the operator's operation training and equipment maintenance records will help to find potential problems and solve them in time.
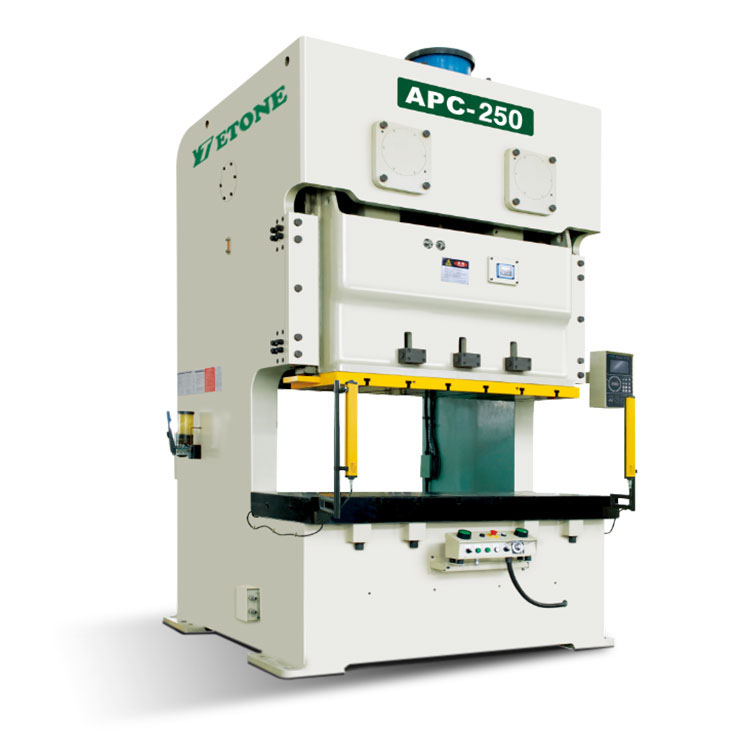