When choosing a double crank stamping punch press model, consider the press's maximum pressure tonnage: Determine the maximum punching pressure required, usually in tons. Choose the appropriate tonnage based on the thickness and type of material being processed.
Table area: Choose a table size that matches your workpiece size to ensure sufficient support surface for stable processing.
Table height: Consider the operator's comfort and choose the appropriate table height.
Stroke depth: Choose the appropriate stroke length to meet the processing needs of the workpiece. Stroke depth affects the maximum processing thickness of the material.
Slider stroke: Check the slide stroke to ensure it is suitable for the processing operation you need. This will affect the processing range and flexibility of the punch press.
Die gap adjustment: Find out if the punch press has a convenient die gap adjustment function to quickly adapt to different dies and workpieces.
Punching accuracy: Choose a high-precision punch press to ensure consistency and accuracy of each punch.
Production speed: Evaluate the punching speed (number of punches per minute) of the punch press to match your production rhythm and efficiency needs.
Drive mode: Double crank stamping punch presses are generally mechanically driven and hydraulically driven. Choose a suitable drive system based on its stability, maintenance requirements and scope of application.
Brand reputation: Choosing a punch press from a well-known brand usually guarantees better quality.
Service network: Make sure the manufacturer provides good after-sales service and technical support. Understand the warranty policy and maintenance services so that problems can be solved quickly when they arise.
Safety devices: Confirm that the punch press is equipped with necessary safety protection devices, such as protective covers, emergency stop buttons, etc., to ensure the safety of operators.
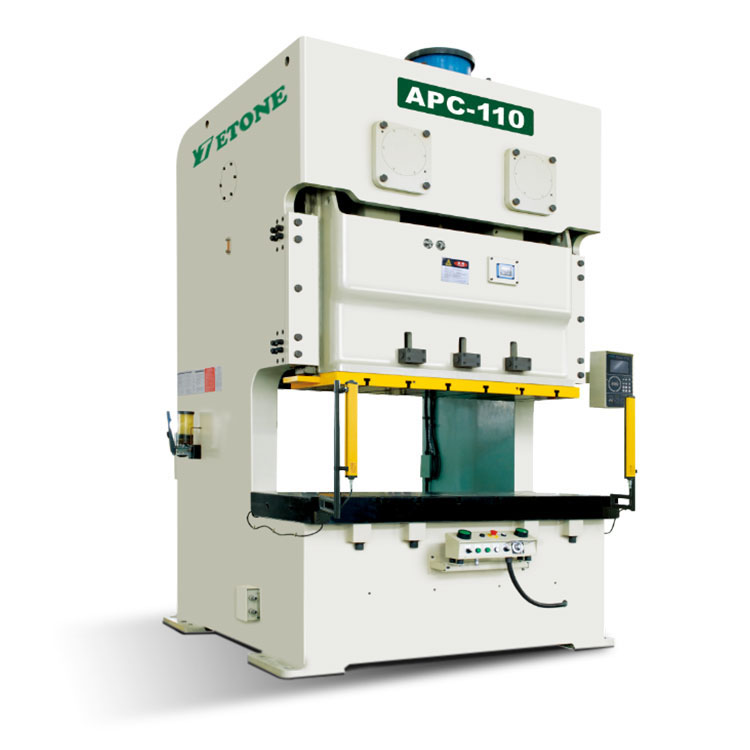